1. Introduction
Cement-based tile adhesive is currently the largest application of special dry-mix mortar. It is composed of organic or inorganic additives such as cement as the main cementing material and supplemented by graded aggregates, water-retaining agents, early strength agents, and latex powders. mixture. Generally, it only needs to be mixed with water when used. Compared with ordinary cement mortar, it can greatly improve the bonding strength between the facing material and the base material. It has good slip resistance and excellent water resistance and resistance. It has the advantages of heat and freeze-thaw cycle resistance. It is mainly used to paste decorative materials such as interior and exterior wall tiles and floor tiles. It is widely used in interior and exterior walls, floors, bathrooms, kitchens and other decorative decoration places. It is currently the most widely used Tile bonding material.
Usually when we judge the performance of a tile adhesive, in addition to its operating performance and anti-sliding ability, we also pay attention to its mechanical strength and open time. Cellulose ether in the tile adhesive not only affects the rheological properties of the porcelain adhesive, such as the operating slip performance, the sticking condition, etc., but also has a strong influence on the mechanical properties of the tile adhesive.
2. Impact on the open time of tile adhesive
The film formation of cellulose ether on the surface of the mortar has a great influence on the performance of the mortar. 1) The film formed is too thin and will be dissolved twice, which cannot limit the evaporation of water and reduce the strength. 2) The formed film is too thick, the concentration of cellulose ether in the interstitial liquid of the mortar is high, and the viscosity is large, and it is not easy to break the surface film when the tiles are pasted. It can be seen that the film-forming properties of cellulose ether have a greater impact on the open time. The type of cellulose ether (HPMC, HEMC, MC, etc.) and the degree of etherification (degree of substitution) directly affect the film-forming properties of the cellulose ether, and the hardness and toughness of the film.
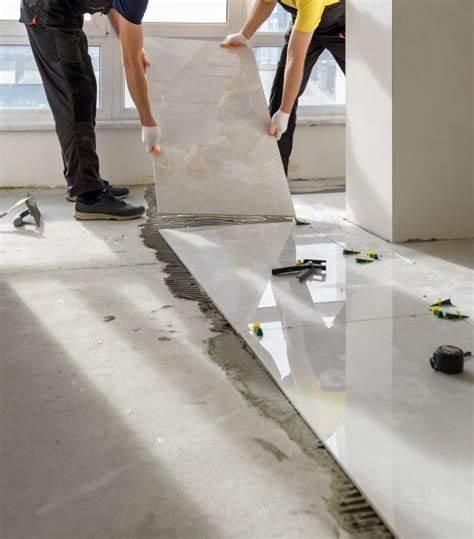
3. Influence on drawing strength
Cellulose ether not only imparts the above-mentioned beneficial properties to the mortar, but also delays the hydration kinetics process of cement. This retardation effect is mainly due to the adsorption of cellulose ether molecules on various mineral phases in the cement system being hydrated, but generally speaking, the consensus view is that cellulose ether molecules are mainly adsorbed on water such as CSH and calcium hydroxide. The chemical products are rarely adsorbed on the original mineral phase of the clinker. In addition, due to the increase in the viscosity of the pore solution, the cellulose ether reduces the mobility of ions (Ca2+, SO42-, …) in the pore solution, thereby further delaying the hydration process.
Cellulose ethers are essential additives in many applications of dry-mix mortar products. The most important property of cellulose ether is its water retention in mineral building materials. If cellulose ether is not added, the thin layer of fresh mortar will dry out quickly, making the cement unable to be hydrated in the normal way, resulting in the mortar being unable to harden and obtaining good adhesion to the base layer.