Cellulose derivatives are widely used in biomedical and pharmaceutical applications. Most signi-
cant from a commercial and technical point of view are cellulose ether and cellulose ether esters.
The common structural element of all cellulose derivatives is the polymeric backbone of cellu
lose, which contains as the basic repeating structure a β-d-anhydroglucose unit with three hydroxyl
groups at the C–2, C–3, and C–6 positions available for substitution.
The nature of the substituent and the number of substituted hydroxyl groups are mainly respon
sible for the individual properties of the different cellulose derivatives like solubility, gelation, or
water retention.
Important substituents are low molecular mass alkyl (ethers) and aliphatic or aromatic carboxyl
ate groups (esters), which are listed in Table 27.1.
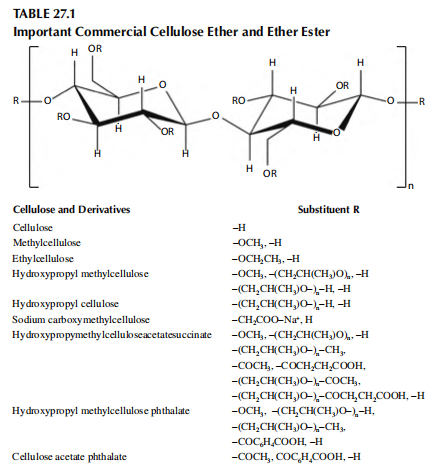
The amount of substituent groups on the anhydroglucose unit is usually designated by the degree
of substitution (DS), the average number of substituted hydroxyl groups with a maximum value of
three or by weight percent.
Hydroxyalkyl substituents are characterized by weight percent or by the molar degree of substi
tution (MS), which is the average number of alkylene oxide reacted with each anhydroglucose unit.
The MS includes also side chain formation due to further etheri cation of hydroxyl groups of the
hydroxyalkyl substituent and may take on any value.
Other characteristics of cellulose derivatives that in uence its properties are molecular weight
(MW), MW distribution, and substituent distribution in and over the polymer chains.
The cellulose ether production process is heterogeneous in nature and consists of two major
steps: an initial mercerization step and the nal etheri cation step. Both steps may be conducted
simultaneously or subsequently. In the mercerization step, the cellulose is being suspended and