II. Materials and experimental methods
II.1. Mineral products
Mortars were prepared according to the CEReM (consortium for study and research on mortars) mixture proportions shown in Table 1 [7]. Mixing procedure was in accordance with EN 196-1 [25]. Admixture amount (0.27%) was in addition to the total dry mixture (i.e. cement, sand and filler). Sand was siliceous and conformed to NF EN 13139 Standard [26] [26], its reference was DU 0.1/0.35. The filler was calcium carbonate (CaCO3). Portland cement CEM I 52.5 R was employed, according to EN 197-1 [27]. Chemical analysis was accomplished by X-ray fluorescence spectroscopy (XRF). Then, approximate phase proportions were calculated using Bogue's formula, with a correction on CaO due to sulfates. The composition of the cement is presented in Table 2. Each experiment was performed three times with the results averaged.
II.2. Organic admixtures
Admixtures are specially prepared products that are added in small amounts to mortar during the mixing process in order to improve its properties.
II.2.1. Starch ethers
Starch is a naturally high-polymeric carbohydrate composed of glucopyranose units bonded together by α-glucosidic linkages. Starch is made up of a linear polymer (amylose) and a branched polymer (amylopectin). Starch ethers are obtained by the reaction of alkyl groups with etherifying agents. In this study, seven starch ethers (SE) were used: two carboxymethyl–hydroxypropyl starches (M1 and M4) and four hydroxypropyl starches (M2, M3, L2 and L3). Properties of the studied starch ethers are detailed in Table 3.
In construction industry, starch ethers enhance workability and improve the application properties of building products.
II.2.2. Cellulose ethers
Cellulose, the most abundant polymer in Nature, occurs mainly within the cell walls of higher plants as a structural material. It is a polysaccharide composed 1,4 glycosidic bonds.-of individual anhydroglucose units linked through β Because of the strong hydrogen bonds that occur between cellulose chains, cellulose does not melt or dissolve into common solvents. Substitution of hydroxyl groups within the cellulose backbone by functional groups provides cellulose with water-solubility through the decrease in the crystallinity of the molecule. The addition of these other groups produces cellulose derivatives like methyl, hydroxyethyl, hydroxypropylmethyl celluloses. In this paper, three kinds of cellulose ethers (CE) were studied: three panels of hydoxyethyl methyl cellulose (HEMC, named as C and TV), two panels of hydoxypropyl methyl cellulose (HPMC, named as J and P), two panels of hydoxyethyl cellulose (HEC, named as H and N). These three CE families are drawn on Figure 1, where substituent positions are arbitrary; they differ from one molecule to another. While the focus of our work is on adding HEMC, HPMC, or HEC to mortars, it is interesting to note that these cellulose derivatives are beneficial and widely used in many industrial fields such as foods, cosmetics, pharmaceuticals, latex paints, construction products, ceramics, and so on. In building domain, cellulose products are used as water retention agents, thickeners, binders, and film formers. To investigate the structural parameter effects, 24 CE were selected (Table 3). Cellulose ethers are defined by three parameters: the average molecular mass (Mw) and two substitution degrees. The number of substituted hydroxyl groups per anhydroglucose unit is expressed as DS (degree of substitution). Moreover, the molar ratio of alkoxy groups in the side chains to cellulose is expressed as the average molar substitution (MS) [28].
HEMC C compounds have a constant chemical structure except for C1; it varies slightly in methoxyl percentage (Table 3). Hence, only the influence of weight average molecular mass on water retention was studied. In the same manner, the molecular weight effect was examined with HMPC J and HEC N for which the substitution degrees are constant among the respective groups. HEMC TV and HPMC P families allowed the investigation of molar substitution impact on mortar's properties.
II.3. Characterization of admixtures
All polysaccharides were characterized by Size Exclusion Chromatography (SEC) in order to obtain their average molecular weight [9], [29] and [30]. SEC analysis was performed on a Waters apparatus equipped with a pump (Waters 916) and a refractometer-type detector (Waters 2410). To study CE and SE, two different columns were used which were the Tosohaas TSK Gel GMPWXL and the OHpak SB-806 M HQ respectively. In our case, the eluent was a 0.5 mol L− 1 sodium chloride solution, it, was filtered and on line-degassed. The flow rate was set to 0.5 mL min− 1 and the column was kept at 35 °C in an oven.
Calibration was performed using standard molecules with known molecular weight and a theoretical polydispersity index close to 1. The obtained peaks established the calibration curve by drawing ln ( MW ) versus the retention time. Subsequently, every chromatogram was divided into slices of hi in height. Thanks to the calibration curve, every retention time corresponded to a mass Mi of Ni molecules eluted of the studied polymer. Every slice height was directly proportional to the concentration ci of the eluted polymer. Therefore, the weight
average molecular mass (noted as MW ) and the number average molecular mass (noted as Mn ) were calculated thanks to the following equations (Equation (1) and Equation (2)).
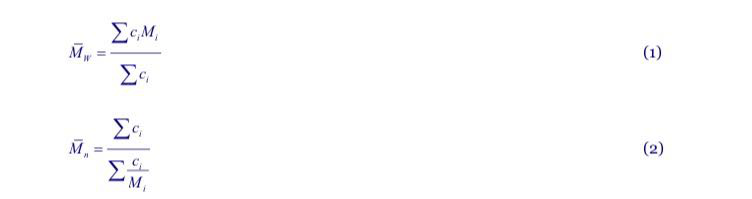
II.4. Water retention measurements
The water retention capacity can be assessed using different test methods. For example, freshly-mixed mortar can be subjected to suction; thereby simulating the action of an absorptive substrate, and the removed water is measured.
A standard method to estimate the water retention capacity of a mortar is the test described in ASTM C1506-09 [31]. ASTM measurements had to be performed 15 min after mixing to measure the water loss of a mortar under depression. The standardised apparatus (Figure 2) was composed of a perforated dish attached to a vacuum assembly by a funnel. The dish was filled in with the freshly-mixed mortar and weighed. The apparatus was exposed to a vacuum of 50 mm of mercury for 15 min.
Then, the water retention capacity, noted WR, was calculated using Equation 3.
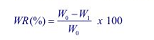
W0 represents the initial mass of mixing water, and W1 is the loss of mixing water mass after aspiration.
A second method was also used to measure the water retention, which is the Standard DIN 18555-7 [32]. With this method, the freshly-mixed mortar was in contact with a filter paper, thereby simulating the action of an absorptive substrate. DIN measurements had to be performed 5 min after mixing. The water retention capacity of a freshly-mixed mortar was characterized by the mass of water it retained after the capillarity action of an absorbent substrate. The standardised apparatus is described in Figure 3. The mortar (3) was poured into the ring. Then, knowing that the water content of the tested mortar was equal to 23 %, for CEReM formulation, the water retention was calculated by weight differences:

where Wfp is the quantity of water retained by the filter paper and W0 is the quantity inside the studied mortar.
All tests were carried out at a controlled temperature (23 °C). This parameter had to be controlled as Hucko has shown that water retention and consistency are temperature- dependent.
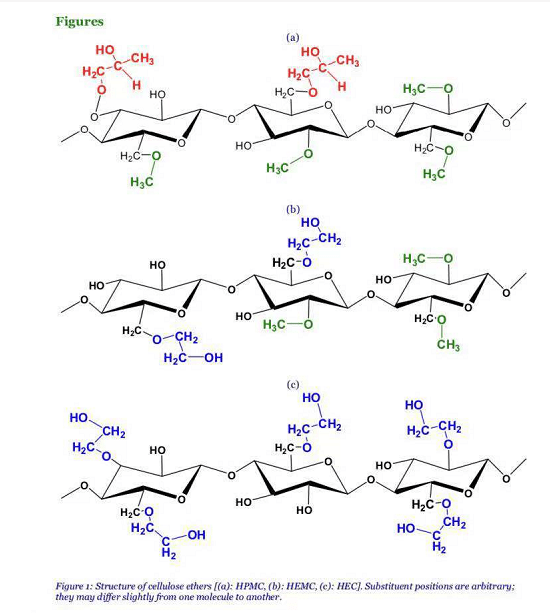
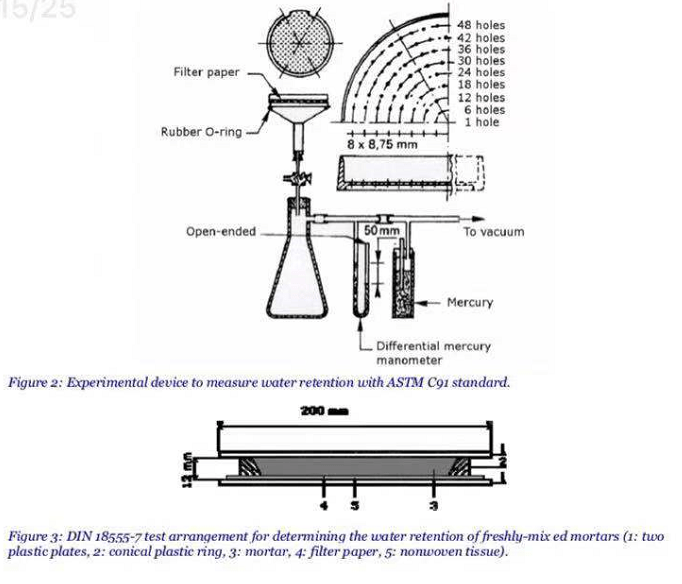
Reference:
[25] EN 196-1. Methods of Testing Cement — Part 1: Determination of Strength (2006).
[26] NF EN 13139. Granulats pour mortiers — Spécifications des caractéristiques des granulats et fillers utilisés dans les mortiers (2003).
[27] EN 197-1. Cement. Part 1: Composition, Specification and Conformity Criteria for Common Cements (2001).
[28] R.L. Feller and M. Wilt, Evaluation of Cellulose Ethers for Conservation, Getty Conservation Institute (1990).
[29] S. Nilsson, L.-O. Sundelöf and B. Porsch, On the characterization principles of some
technically important water soluble non-ionic cellulose derivatives, Carbohyd. Polym.28 (3) (1995).
[30] C. Clasen and W.-M. Kulicke, Determination of viscoelastic and rheo-optical material functions of water-soluble cellulose derivatives, Prog. Polym. Sci. 26 (9) (2001).
[31] Standard C1506-09 , Standard test Method fo Water Retention of Hydraulic Cement- Based Mortars and Plasters, Am. Soc. Test. Mat. (2009).
[32] Standard DIN 18555-7, Testing of Mortars Containing Mineral Binders; Part 7Determination of Water Retentivity of Freshly Mixed Mortar by the Filter Plate Method, Deutsches Institut für Normung (2000).