The terms defoamer and anti-foam agent are often used interchangeably, but they in fact differ. Defoamers eliminate existing foam, while anti-foamers prevent the formation of more foam. Antifoams are typically added to the foaming solution before foam formation and act to avoid excessive foam formation. In contrast, defoamers or foam breakers are substances sprinkled over existing foam, aiming to induce rapid foam collapse. In industrial processes, foams may create serious problems. They can cause defects on surface coatings and stop the efficient filling of containers. Many different chemical formulae are available to avoid the formation of foams.
How Defoamers and Antifoaming Agents Work
A vital feature of defoamers is the ability to spread rapidly on foamy surfaces. Another feature is partial solubility. A defoamer must not be too dispersible or too soluble. If it goes too far in either direction, it will not break up foam and may even contribute to additional foam build-up.Furthermore, defoamers must have low surface tension so that they can spread rapidly along the surface interface to achieve maximum interaction with the foam. As an effective defoamer disperses, it must be capable of displacing the foam-stabilizing surface-active components and penetrating the foam's lamellae to allow the entrapped gas to escape and the foam to burst.
They function by entering the interface between the air and foam's lamellae. The antifoam penetrates the bubble wall, which is bridged by the antifoam droplet. This is called "bridging of the film." As the antifoam spreads, the bubble wall is thinned. Once the antifoam has entered the lamella, it forms a lens on the lamella and begins to spread. The progressive spreading process reduces the lens's thickness, which is altered by movements in the foam. Stresses occur until the lens breaks and the foam lamella ruptures. The resultant film is considerably less elastic than the surfactant film, which previously stabilized the lamella. This destabilization facilitates the rupture of the lamella.
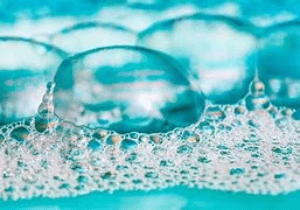
Applications
Anti-foams are added to some detergents to reduce foaming, which might decrease the action of the detergent. Dishwasher detergents, for example, have to be low foaming for the dishwasher to work correctly. When used as a food ingredient, antifoaming agents control foam or fizziness in preparation or serving. They are included in a variety of foods and materials for food preparation. McDonald's uses polydimethylsiloxane, a type of silicone antifoaming agent, in its oil to mitigate hazardous splashes of oil caused by foaming in fryers, so it has been listed as an ingredient in their fried menu items.Defoamers are used in various industrial processes and products, including paper, wood pulp, paint, industrial wastewater treatment, machine tools, food processing, oil drilling, oils cutting tools, and hydraulics. Antifoaming agents are also sold as drugs to relieve bloating. One example is the drug Simethicone, which is the active ingredient in drugs such as Maalox, Mylanta, and Gas-X. Anti-foamers are often added to paints, inks, coatings, and additives. The mixing, grinding, and chemical reactions involved in producing these materials can create foam, leading to increased production times, reduced operational efficiency, and defects in the physical product. To prevent this, antifoam is used in applications including polymer and pigment grinding, package filling, and shearing or spraying